Enhancing the durability and longevity of CNC machined bike handlebars, especially for demanding riding conditions, involves several measures and considerations:
1.Material Selection:
Aluminum Alloys: Utilizing high-grade aluminum alloys such as 6061 or 7075, known for their exceptional strength, corrosion resistance, and lightweight properties. These alloys are ideal for withstanding the stresses encountered during rigorous cycling activities.
Titanium: For premium applications, titanium is chosen due to its outstanding strength-to-weight ratio, corrosion resistance, and fatigue endurance, ensuring longevity under extreme conditions.
Carbon Fiber Composite: Implementing advanced carbon fiber composites that offer remarkable strength and stiffness while being lightweight, making them ideal for high-performance handlebars.
2.Heat Treatment:
Applying heat treatment processes such as T6 tempering for aluminum alloys to enhance their hardness and mechanical properties. This treatment minimizes deformation and increases resistance to wear and fatigue, crucial for prolonged durability.
3.Precision Machining:
Utilizing CNC machines equipped with high precision and multi-axis capabilities to achieve intricate shapes and dimensions accurately. Precision machining ensures uniform material distribution, reducing weak points and vulnerabilities in the handlebar structure.
4.Stress Analysis:
Conducting finite element analysis (FEA) and stress simulations to identify stress concentration areas. Engineers optimize the handlebar's design, redistributing stress to prevent localized wear and failure points, thereby increasing its longevity.
5.Surface Finishing:
Employing surface finishing techniques such as anodizing, which not only provides a corrosion-resistant layer but also enhances surface hardness and wear resistance. Powder coating or specialized coatings can also be applied to improve aesthetics and protect against environmental factors.
6.Reinforcement:
Incorporating internal reinforcements, such as strategically placed ribs or honeycomb structures, to augment strength without significantly increasing weight. These reinforcements distribute forces evenly, improving overall structural integrity.
7.Impact Testing:
Subjecting prototypes to impact testing using controlled methods and simulations that replicate real-world scenarios. This testing helps validate the handlebar's ability to absorb shocks and impacts without compromising its structural integrity.
8.Vibration Damping:
Introducing vibration damping technologies, such as elastomeric inserts or composite layers with vibration-absorbing properties. These features reduce the vibrations transmitted to the handlebar, decreasing fatigue and enhancing longevity.
9.Quality Control:
Implementing rigorous quality control processes, including visual inspections, dimensional checks using precise measuring tools, and non-destructive testing techniques like ultrasonic testing. These measures ensure that every handlebar meets strict quality standards before reaching the market.
10.Compliance with Standards:
Adhering to industry standards and safety regulations, such as ISO 4210 for bicycles, to guarantee the handlebars' compliance with safety norms. Compliance ensures that the handlebars are designed and manufactured to withstand various stresses and loads experienced during cycling.
11.User Feedback:
Actively seeking feedback from professional riders, cycling teams, and enthusiasts. This valuable input helps manufacturers identify potential issues, preferences, and areas for improvement, leading to iterative design enhancements.
12.Regular Maintenance Guidelines:
Providing users with comprehensive maintenance guidelines, including recommended torque specifications for bolts and periodic inspection protocols. Educating users on proper care and maintenance prolongs the handlebar's lifespan and ensures safe usage.
Q-05 Aluminum Alloy CNC machining TT handlebar bike handlebar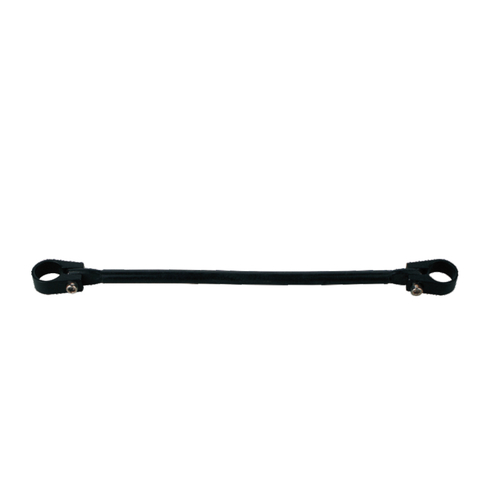